Product overview
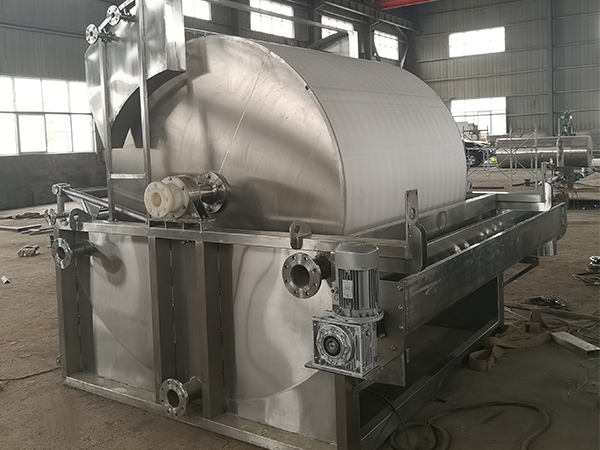
Vacuum rotary filter belongs to the continuous operation type filtration device, which can achieve solid-liquid separation with the help of the strong driving force formed by the negative vacuum pressure. In the operation of the equipment, the suspension is introduced into a specific processing area, under the action of vacuum negative pressure, the suspension of liquid can smoothly penetrate the filter media, such as filter cloth is one of the commonly used filter media. And solid particles will be intercepted by the filtration medium, and gradually accumulate to form filter cake.
The core component of the vacuum rotary filter is a rotatable cylinder, also known as the rotary strand. The rotor is partially submerged in a slurry tank, covered with a filter cloth, and is internally connected to the vacuum system and compressed air system by means of a distributor head. As the rotor continues to rotate, a series of key processes such as filtration, washing, dewatering and cake removal are completed, ensuring that the entire filtration process is carried out in a more efficient and continuous manner.
Features of vacuum rotary filter
Continuous and efficient output:
It can operate continuously, realize uninterrupted production, shorten the production cycle significantly, reduce the loss of equipment start and stop time, significantly improve the production efficiency, and satisfy the demand of large-scale industrialized production on the output.
Depth and pure separation
Good washing effect of filter cake, uniform distribution of washing liquid to ensure full and thorough washing. Precise control of washing parameters can effectively remove impurities and soluble substances from the filter cake, realizing solid-liquid separation with high purity and guaranteeing product quality.
Accurate and flexible adaptation
Highly adjustable, the operator can accurately adjust the drum speed, vacuum and other key parameters according to the material characteristics, process requirements and production conditions, to adapt to complex working conditions and stabilize the filtration effect.
Compact and space-saving
Compact and reasonable structural design, scientific layout of components and integration of various functions. Compared with traditional equipment, it occupies a small area, which is conducive to optimizing the layout of the workshop, improving the utilization rate of space and reducing the site cost.
Vacuum Rotary Filter is widely used in chemical, mining, food, environmental protection and other industries, and it is more suitable to be used to deal with suspensions with high concentration and moderate granularity. The equipment through automated continuous operation, can produce stable output of high dryness of the cake, and filtration efficiency by the slurry nature of the fluctuations of the influence of less, is the industrial solid-liquid separation of one of the important equipment in the field.
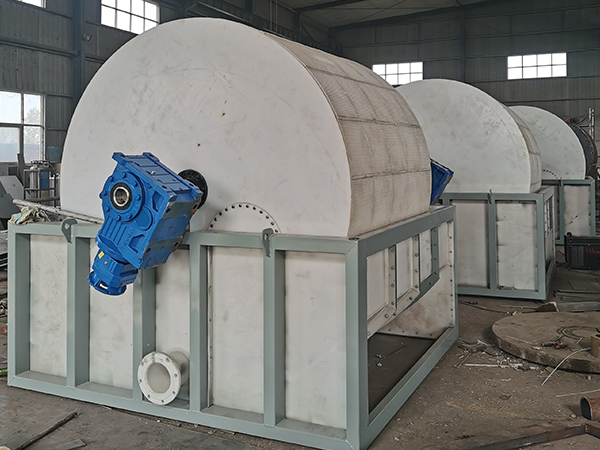
Composition and structure of vacuum strand transfer filter
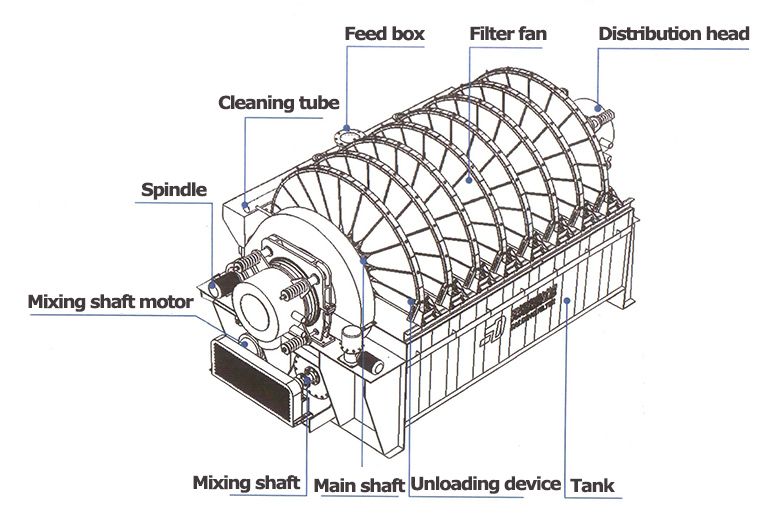
Strand transfer:
Cylindrical structure, the material can be selected according to the actual working conditions. For example, in the general environment, stainless steel, cast iron, plastic, etc. are commonly used materials
In more corrosive environments, in order to ensure the durability and stability of the equipment, titanium alloys or rubber lining process is usually used.
The surface of the rotary strand is evenly distributed with filter chambers, each of which is connected to the distributor head inside the rotary strand through a special pipeline, thus ensuring a smooth material transfer during the filtration process.
Dispensing Head:
The dispensing head is the key component inside the drum and consists of a fixed disk and a rotating disk. By means of the synergistic action of these two disks, the rotating process of the drum is precisely divided into different working zones, including the filtering zone, the washing zone, the dewatering zone and the cake unloading zone.
The distribution head is also connected to the vacuum system and the compressed air system respectively. During the filtration, washing and dewatering stages, the distributor head is connected to the vacuum system to provide the necessary negative pressure environment for these processes.
Slurry Tank:
The main function of a slurry tank is to hold the suspension to be filtered. In order to prevent the slurry from settling in the tank, some machines are equipped with a stirring device to ensure that the slurry is always homogenized.
In addition, depending on the filtration requirements, the slurry tank can be designed with heating or cooling jackets. In this way, both high-temperature and low-temperature slurries can be effectively filtered in this equipment, greatly expanding the scope of use of the equipment.
Filter Media:
Usually, the filter media is selected from filter cloth, the common filter cloth materials are polyester, polypropylene, nylon and other synthetic fiber cloth, and metal mesh will also be used in specific cases. The selection of the filter cloth takes into account the size of the solid particles in the slurry as well as the chemical properties.
The filter cloth is firmly fixed on the surface of the drum, with the use of time, the filter cloth may be clogged or worn and affect the filtration efficiency, so it needs to be cleaned or replaced periodically to ensure the normal operation of the equipment and filtration effect.
Auxiliary system:
Vacuum system: this system mainly consists of vacuum pump and vacuum tank, whose function is to provide negative pressure power for the equipment. In actual operation, the vacuum is generally controlled between 0.04 - 0.08 MPa to ensure that the filtration process can be stable and efficient.
Compressed air system: the main purpose of this system is to play a role in the stage of unloading the cake, by blowing compressed air to the cake, so that the cake and the filter cloth are separated, so as to facilitate the operation of unloading the cake.
Washing device: The washing device adopts the design of spraying system, which can evenly spray the washing liquid on the surface of the filter cake to effectively reduce the content of soluble impurities left in the filter cake and improve the purity of the product.
Cake unloading device: The cake unloading device usually adopts the form of scraper or belt. The scraper can scrape the dewatered filter cake directly from the filter cloth; the belt will strip the filter cake from the filter cloth through its own movement to realize the smooth discharge of the filter cake.
Benefits of using vacuum rotary filters
In the entire operation process does not require frequent start and stop, effectively reducing the frequency of manual intervention, can seamlessly adapt to the rhythm and requirements of large estimation of industrialized production. In a long time, large quantities of production tasks, not only improve the production efficiency, but also significantly reduce labor costs, saving money for the enterprise.
The filter cake obtained after treatment by the equipment, the dehydration effect is relatively good, the water content can usually be controlled at a lower level of 10% -30%, at the same time, in the washing process, the equipment can ensure that the washing liquid is uniformly acted on the filter cake, so that the residual filtrate is greatly reduced, which a series of advantages effectively enhance the purity of the solid product, to ensure that product quality, stability and consistency.
It can easily cope with a variety of different types of suspension processing tasks, whether it is a high annual slurry, or a complex suspension containing a small amount of fiber, it can handle. Moreover, by flexibly adjusting the operating parameters of the equipment, such as the rotational speed of the drum, the vacuum generated by the vacuum system, etc., you can accurately meet the specific needs of solid-liquid separation in different scenarios, and truly realize a multi-purpose machine.
Compared with the pressurized filtration equipment, the vacuum system used in the equipment has obvious advantages in energy consumption. The vacuum system consumes relatively less energy in the operation process, which can effectively reduce the energy cost of the enterprise. In addition, the maintenance cost of the equipment is also lower, its structure is reasonably designed, the durability of the parts is stronger, reducing the trouble of frequent maintenance and replacement of parts, further saving the operating costs for the enterprise.
The equipment has a good closed, in the process of operation can effectively avoid the splash of slurry and the spread of odor. It effectively improves the operating environment of the workshop and reduces the chances of the staff coming into contact with harmful substances. At the same time, the neat and orderly workshop environment also helps to improve the image and management level of the enterprise.
Advantages of Vacuum Rotary Filter
Compared with other filtration equipment, the core advantages of vacuum rotary filters are:
Comparison term | Vacuum rotary filters | Plate and frame filter | Centrifugal filters |
Operating method | Continuous operation | Intermittent operation | Continuous/intermittent |
Degree of automation | High | Relatively low | Higher |
Cake dryness | Higher | High | High |
Treatment capacity | Large | Medium | Large |
Requirements for slurry stability | Lower | Higher (prone to clogging) | Higher (viscosity sensitive) |
Power consumption | Lower | Medium | High |
Vacuum rotary filters have better cake washing effect, especially suitable for processes requiring multi-stage washing, and the equipment runs with low noise and is easy to maintain.
Vacuum rotary filter manufacturer
Equipment selection and customization: according to the user's slurry nature and production needs, to provide personalized design solutions;
Installation and commissioning: a professional team to assist in the installation of equipment, debugging parameters, to ensure that the filtering effect is achieved;
Spare parts supply: the provision of filter cloths, distributor head seals, vacuum pump wearing parts, etc., to ensure that the equipment continues to run;
Technical support: regular return visits, fault repair, equipment registration Technical support: regular visits, fault maintenance, equipment registration.
Hot Tags: