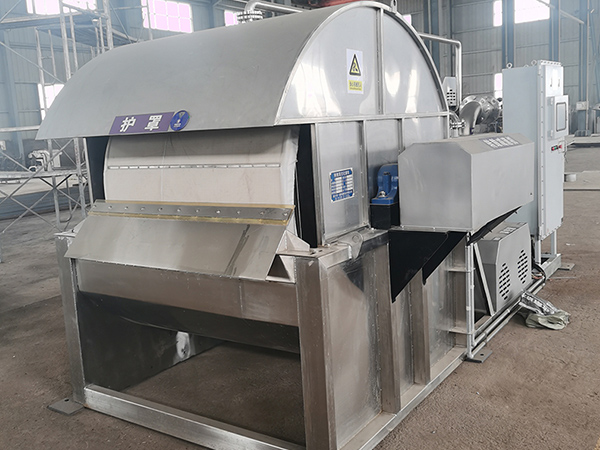
Introduction to Rotary drum filter
The Rotary drum filter is a solid-liquid separation device that relies on vacuum suction as the driving force, and its core component is a cylindrical rotary strand that can rotate continuously. The device utilizes the rotary motion of the rotating strand to drive the filter media covering its surface to complete a series of key operational steps in sequence. From the initial filtration of the suspension, to the deep washing of the filter cake, to the strong suction removal of excess water, and finally realize the automatic stripping of the filter residue is discharged. This series of processes are seamlessly connected in the continuous rotation of the rotating stock, forming an efficient and stable cycle production mode. It is very suitable for chemical, food, pharmaceutical processing and other industrial scenarios that require large-scale, continuous processing of suspension materials.
Working Principle
The working mechanism of the rotary vacuum filter is based on the synergistic effect of negative vacuum pressure and rotary strand rotation, which realizes efficient solid-liquid separation of suspension through dynamic circulation, and its complete operation process includes.
Vacuum filtration stage
The rotating stock enters the suspension, the vacuum system makes the pressure difference between the two sides of the filter cloth, the liquid phase penetrates the filter cloth and enters the rotating stock, and the solid phase is retained to form the filter cake.
01
Reverse washing
After the rotating strand turns out of the filter surface with the filter cake, the washing liquid penetrates the filter cake by spraying or submerging, and the vacuum suction draws off the dissolved impurities to realize deep purification.
02
Vacuum drying
The drum continues to rotate to the drying area, strengthening the vacuum effect to further remove the residual liquid phase in the capillary channels of the filter cake, reducing the moisture content.
03
Mechanical unloading
When the drum enters the unloading area, the vacuum is released and combined with the compressed air blowback or scraper stripping, so that the filter cake is completely removed to the hopper.
04
Regeneration of filter cloth
After unloading, the filter cloth is blown by high-pressure spray or compressed air to remove the pores and surface residual particles, restore the filtration performance and enter the next cycle.
05
Structure
Rotary drum filter is mainly composed of the following key components:
Rotary Unit
The core of the equipment, usually cylindrical metal cylinder, the surface is densely covered with microporous to adsorb liquid. Internal division of a number of independent fan-shaped compartments to achieve process partition control.
Filter cloth
The filter layer covering the surface of the rotating strand, the material is selected according to the characteristics of the material, used for retaining solid particles.
Material tank
The suspension container placed under the drum, the lower part of the drum is immersed into the tank with adjustable depth to ensure continuous contact with the material to be filtered.
Vacuum system
It is composed of vacuum pump and vacuum tank, providing negative pressure power for filtration, washing and drying stages, and driving the liquid to penetrate the filter cloth.
Washing device
Equipped with a spray pipe or soaking tank, located in the area of the liquid surface of the drum, used to spray washing liquid such as water or solvent to the filter cake.
Slag removal components
Including metal/rubber scraper and compressed air blowback system, the synergistic effect of the filter cake from the surface of the filter cloth stripped off.
Transmission mechanism
By the motor, reducer and gear / chain transmission group, drive the drum to 0.5-3 rpm uniform speed rotation.
Distribution head
Distribution head: Dynamic valve installed at the end of the drum, rotating with the drum, connecting different compartments to the vacuum or compressed air system through the pipeline, realizing automatic process switching.
Advantages of rotating drum filter
Continuous operation
Continuous rotation of the rotating strand to realize the automation of the whole process of filtration, washing and discharging, which greatly improves the efficiency of large-scale production.
A high degree of automation
Through the adjustment of rotating strand rotation speed, vacuum, and the washing liquid parameter, it ensures the stable and controllable filtration quality, and significantly reduces the dependence on manual operation.
Good cake washing effect
It supports the design of multi-stage reversed washing. Effectively reduce the residue of soluble impurities in the filter cake to meet the demand for high-purity products.
Wide range of application
It can deal with suspensions of different concentrations and particle sizes, and is especially suitable for material systems with medium concentration and good particle settling performance.
Usage of Rotary Vacuum Drum Filter
Rotary drum filter are mainly applied to deal with suspensions with high concentration, coarse particles, easy cake formation and easy discharging, and the main application areas are
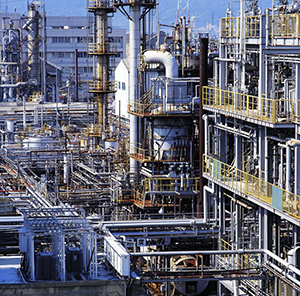
01
Chemical industry
Applied to the production of pigment, dyestuffs, catalysts, fertilizers, and caustic soda, etc., to efficiently separate solid-liquid mixing system after the reaction.
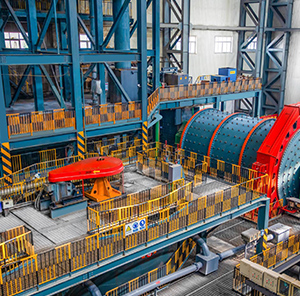
02
Mining processing
For gold, copper, iron and other slurry processing, to achieve effective recovery and purification of solid minerals.
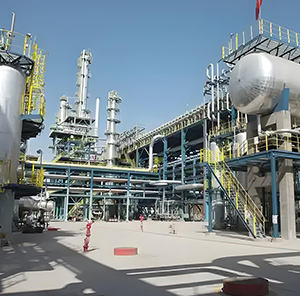
03
Environmental protection
For printing and dyeing wastewater, chemical sludge and other industrial waste, to achieve efficient dehydration and solid-liquid separation.
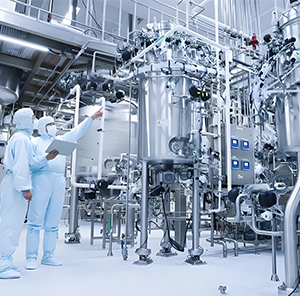
04
Pharmaceutical production
In the process of API preparation, to complete the key solid-liquid separation process, the equipment needs to meet the sanitary manufacturing specifications.
Common faults and solutions of rotating drum
filter
Fault phenomenon | Possible reasons | Solution |
The filtration speed suddenly decreases | Filter cloth is blocked; vacuum degree is insufficient; suspension concentration is too low | Replace or clean the filter cloth; check if the vacuum pump is functioning properly, and repair any air leaks; adjust the suspension concentration (e.g., by adding flocculant) |
The thickness of the filter cake is uneven | The rotary drum is rotating too fast; the liquid level in the trough is unstable; the filter cloth is deviating | Reduce the rotational speed; adjust the feeding speed to stabilize the liquid level; calibrate the position of the filter cloth and check the tensioning device |
The filter cake cannot be removed | The vacuum degree is not cut off in time; the scraper is worn or the angle is improper; the filter cake is too dry/too sticky | Check whether the distribution head switches normally (cut off the vacuum); replace the scraper or adjust the angle; adjust the vacuum level or the amount of washing liquid |
Insufficient vacuum degree | Vacuum pump malfunction; pipeline or compartment air leakage; filter cloth damage | Overhaul the vacuum pump; inspect the pipeline connections and the sealing of the drum compartment, repair any leaks; replace any damaged filter cloth |
Poor washing effect | Insufficient flow of washing liquid; blocked spray pipe; too short washing time | Increase the flow rate of the washing liquid; clean the nozzles of the spray pipe; reduce the rotational speed of the drum and extend the washing time |
Abnormal noise during equipment operation | Bearing wear; transmission gear/chain looseness or insufficient lubrication | Replacethebearing;tightenthetransmissioncomponents,andaddlubricatingoil |
By regularly inspecting the condition of the filter cloth, the tightness of the vacuum system, and the wear of transmission components, the occurrence of malfunctions can be effectively reduced, ensuring stable operation of the equipment.
Rotary drum filter Price
The price of a rotary vacuum drum filter is affected by a number of factors. The filtration area is an important factor, from the laboratory use of small equipment to industrial use of large equipment, the larger the area, the higher the price amount. The material of the equipment is also related to the cost, when contacting corrosive materials, the use of acid and alkali resistant special alloys or engineering plastics, the cost is relatively high.
Choose us as your rotating drum filter manufacturer, we rely on years of industry experience, advanced production technology and the pursuit of innovation, to create a highly efficient and reliable filter, to provide a solid guarantee for your production process.
Hot Tags: